A top-level overview on some considerations to hold while designing 3D printed parts for FDM machines.
3D printers are incredibly powerful tools for prototyping and design. A thousand-dollar 3D printer can create components that would be impossible for multi million-dollar CNC milling machines. That said, they aren’t magic. They can’t simply conjure into existence anything you could possibly imagine, at least not without some constraints. There are design considerations to heed, limitations to consider, failure points to avoid. This guide will provide a few things to keep in mind when designing parts for 3D printing.
I have loosely organized these points in terms of how crucial they are to consider. First are those considerations that could fail the print entirely if not heeded, then those that may simply create a part that does not work as expected, and then finally a few ways to fine-tune your component and have it be the best part your printer can create.
Also, to clarify, this article focuses specifically on Fused Deposition Modeling (FDM for short) printing. Stereolithography Curing and Laser Deposit printing are fascinating technologies, but they will have different limitations and capabilities.
So without further ado, let’s start with the most vital considerations:
Fundamental Considerations
(Factors that can kill the print)
Overhang angle
Many 3D printers, especially FDM printers, can only reach out so far beyond the layer below them before they start to spill over and cause a mess. This is simply because, as it extrudes plastic, that plastic needs something to sit on in the few moments before it solidifies onto the part. Different materials and printers result in different maximum overhang angles, and usually the most efficient way to tell what your maximum overhang angle is would be to print a test part designed for the purpose and see at what angle it begins to fail.
Failing to heed overhang angle constraints in one’s designs can lead to what are commonly known as “angry spaghetti”.
The extruder attempts to print material onto what it expects to be a supportive surface, but due to either the material failing to stick, or that support material simply not existing, it instead just extrudes the molten plastic directly into the air below it. The missed layers can lead to more missed layers printed above it, causing the print to potentially fail entirely beyond that first overhang point. If the print is left unsupervised, it will just keep running until it thinks its completed, and you will return to find a half-finished part and a horribly tangled mess of filament material to clean up afterwards. Take my word for it, angry spaghetti failures are well worth avoiding if at all possible.
Support material can often help with overhang angles, though if the overhanging surface is large, it might end up demanding quite a lot of material to keep things well-enough situated. It’s best to design for minimal overhang angles if at all possible.
Bridging / Arches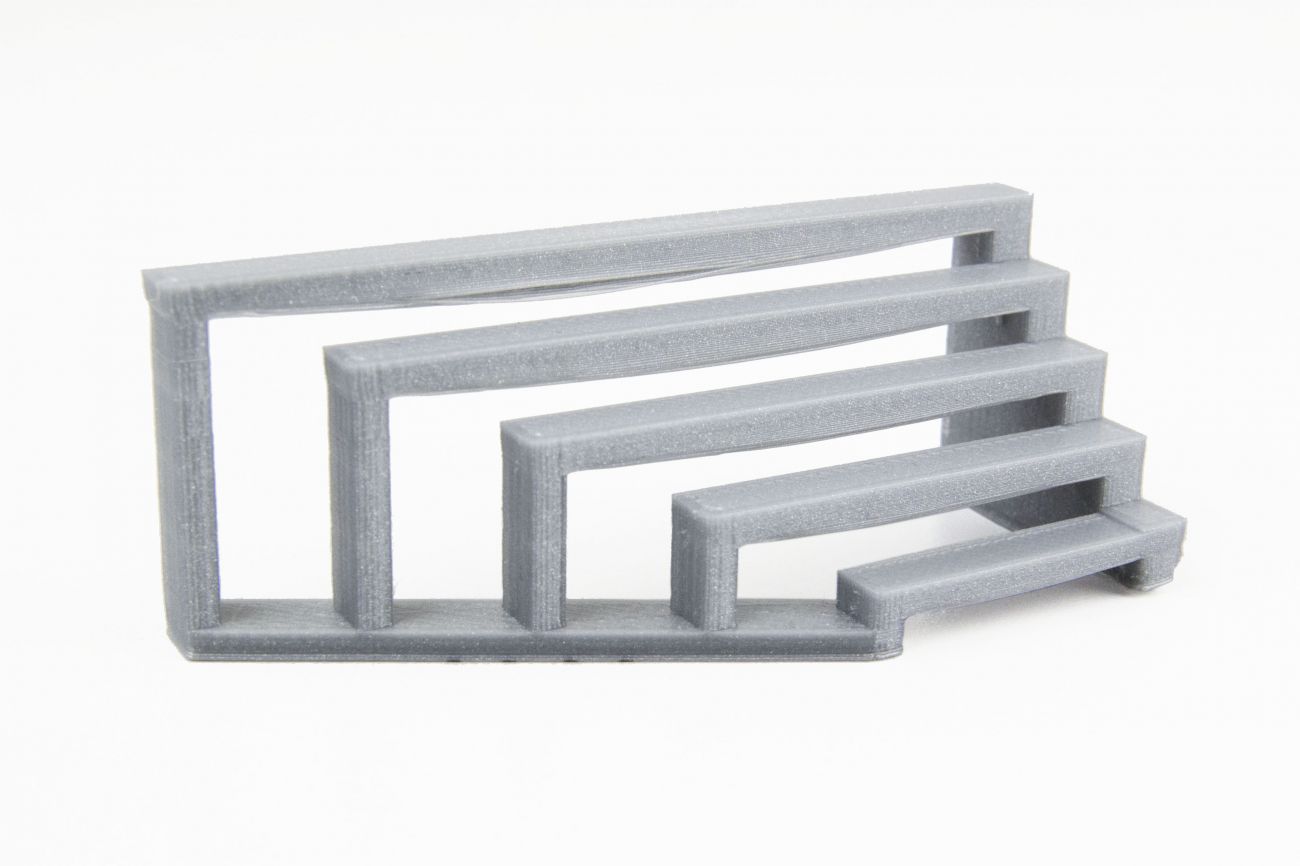
Bridging is what happens when a 3D print requires material to be extruded over an open gap, as pictured above. For very short distances, this is usually no problem, for much the same reason that extruding toothpaste across the bristles of your toothbrush doesn’t make it fall into the crevices. But if you stretch too far between contact points, that bridging can cause the lower filaments to stray a bit, as shown in the image above, or even generate angry spaghetti failures.
As with overhang angle, failures can usually be prevented with well-placed support material, but it might demand quite a bit of support if not carefully designed.
Arches are similar to both bridging failures and overhang angle failures. They appear in, well, arches. Two or more separate sections of plastic merging into one, usually over a circular void. It leaves a horizontal point at the top that is prone to suffering from both overhang and bridging types of failures, potentially including angry spaghetti. Arches often suffer overhang issues along the top before reaching the bridge, but the two problems can be quite similar.
Arches. And, as with bridging, a sufficiently wide span might demand quite a lot of support material to resolve the issue.
Arching can also be solved with supports, but another effective resolution is simply to change the shape of the arch in question. If you make teardrop shaped arches, as shown below, where the angle of the faces is within the overhang angle limit, then you won’t need any support at all to print that portion of the design.
Wall Thickness / vertical pillar diameter
One last design consideration that could result in total print failure is thin vertical walls or vertical pins that are too thin for their height. With such designs, there’s a chance that the wall or pin might warp away from the print head and create an angry spaghetti situation. But, if it doesn't it still tends to deviate from its expected path significantly enough to result in a very rough outer wall, as shown below. This is simply because, as the thin wall gets taller and taller, it tends to flex more and more under the accelerations of the print bed, and the print head fails to print in exactly the right location relative to the existing plastic. Then on the next pass, the wall not only deflects from where it ought to, but also the last layer was in the wrong location, so it prints a line even further from the expected path. Such errors can compound and cause significant problems for the print, as seen below. They can even generate angry spaghetti failures if things get bad enough.
An additional point to consider is whether the printer can actually produce a wall that thin. If you ask for a wall 0.5mm wide, and the extruder spits out material 0.75mm wide due to its shape, then there is simply no way for it to possibly make a wall that thin, potential design failures aside.
Thin pillars printed vertically will often suffer a similar sort of error to thin walls. The image below shows the compounding error problem with greater clarity than with the thin wall example above.
Support material, as with most 3D print problems, can minimize or entirely mitigate these sorts of errors. But often a simpler solution for thin pillars and walls is simply to thicken them a little, if possible Thicker pillars/walls will deviate less from their expected location the further up they go, and therefore are less prone to this sort of error.
Important considerations
(won’t kill the print, but final part might not work as intended)
Internal hole diameters / interlocking part sizing
The nature of FDM prints forces a certain amount of excess material beyond the bounds of the original print. This is a necessary part of how 3D printers print material, as it allows the user to sand the final product down to more precise tolerances. However, this does mean that flush-fit components become much harder to design.
The most common situation where this issue emerges is with internal holes, where the excess material spilling over causes the effective diameter of the part to be smaller than was originally designed for. Below is a representation of how the excess material from each layer causes the final diameter of the print to shrink.
To design interlocking components with specific tolerances between them, you must account for how much extra material is extruded beyond the designed bounds. This varies by material and printer, but 0.015 to 0.02in is often a reasonable assumption if you have no other information upon which to base your guess.
This became a problem with our recent Egg Smash Challenge here at CADimensions. Team 2's design required a protective plate to slide into slots connecting it to the main structure. Though the original design did provide 0.02in of extra space between the tabs and the slots, the material spillover was greater than anticipated, and quite a bit of sanding needed to be done before it could fit together as intended.
Minimum Detail Size
Stereolithography and Laser Sintering printers are wonderfully advanced technologies capable of producing parts with incredibly tight tolerances. FDM printers, generally, are not. This is a significant reason that FDM printers tend to have a zero or two fewer in their price tags. And unfortunately, that is an important factor to consider when designing 3D printed components. There is a minimum size at which details will simply not appear as legible within a print. It's important to know what that size is, and to create your parts accordingly.
In the image below, the goblin on the left was printed with a FDM printer, while the one on the right was printed with a stereolythography printer. Notice how the gray goblin, though smaller, is much more visually legible and cleaner than the one on the right. The white goblin is a good example of a design too detailed for the printer it was used for.
Model Splitting
Sometimes, for a variety of reasons, it's wiser to split your model into multiple, separate prints rather than try and create them all at once. Perhaps the final product is too large to fit into one print bed, sometimes different parts of the design require different layer orientations, sometimes that's just the easiest way to minimize necessary support material.
For Team 2's Egg Protection design, the shear plate described above in the Interlocking Parts section was meant to take the brunt of the impact from a falling brick. As such, it was important that the print layers remain parallel to the bulk of the plate surface for maximum strength. As a result, it needed to be printed separately. So we designed it separately, and accounted for how it would interlock with the main structure accordingly.
We also designed the egg cradle component separately from the main chassis for ease of adding the egg to the design, and to allow the main base of the structure to bounce away from the part containing the egg if need be.
Material and Mesh Density
If factors such as mass, material strength, and other material properties are a concern for your part, you should account for the intended material and mesh density within your part design. One of the constraints for our Egg Protection Challenge was to keep the entire design under 500g, using Nylon-CF-10, a nylon-based material infused with 10% carbon fiber for added material strength. Additionally, we were required to use 100% infill on the design. It was a challenge keeping the design within the given mass limits, but our final print came in at 485 grams.
Advanced Considerations
(Fine tuning the part to come out as perfect as possible)
There are quite a few further factors to consider when designing for 3D printing specifically. Here is a short list of considerations that I will elaborate upon in a later article:
- Elephant's Foot
- Warping
- Layer orientation / Support Material Minimization
- Selection of Bottom face of the part
- Seam closing
- Rounding corners during printing for a cleaner final product
- Fillets for strength
- Ribs for strength
- Orientation to Minimize Support Material
As always, if you have any technical issues or questions about 3D printing, Solidworks or other related concerns please feel free to reach out to our Support page.