This article discusses how to create and utilize sheet metal bend tables in SOLIDWORKS.
How To Properly Configure a Bend Table
SOLIDWORKS includes sample bend tables with the software, but it is incumbent on the end user to make sure they are accurate and will fit in with the manufacturing techniques being employed. One such bend table is shown (in part) in Image 1. The default location for bend tables is "C:\Program Files\SOLIDWORKS Corp\SOLIDWORKS\lang\english\Sheetmetal Bend Tables". Your SOLIDWORKS installation location, and therefore your bend table location, may be different.
Image 1: Sample Bend Table included with SOLIDWORKS.
Using Empirical Data
There are a few empty bend tables included with the software. These are useful because the formatting is already set up. All that is left is to plug in the desired data. The upper portion of the Base Bend Table is shown in Image 2. The Unit and Type values are read from the table and should only be certain values. Available values are listed in the header after the number (#) sign, which can be seen in the image.
Image 2: A portion of the "Base Bend Table".
The number sign (#) used in tables indicates to SOLIDWORKS that anything which follows is a comment or for reference only. It will not attempt to process anything which follows the pound symbol.
Obviously, with the Base Bend Table shown above, it is necessary to fill in data. It is perfectly acceptable to strip out rows or columns if they are not needed, but this is not necessary and can actually lead to problems. The following section shows an example of why that is the case.
Common Bend Table Errors
When using bend tables, one very common error is as follows:
"Warning: The thickness of this bend fell outside the bend allowance/deduction table. The bend allowance/deduction is evaluated using the K factor instead."
Let's imagine a company that only uses .03125" thick sheet metal with a .0625" bend radius and 90 degree bends. They have determined the manufacturing process requires a bend allowance of .035". They have stripped everything out of their bend table to make it very simple. Their bend table looks like Image 3.
Image 3: No margin for error!
The designer creates the model in SOLIDWORKS. During this process, they enter the sheet metal parameters in the Sheet Metal PropertyManager show in Image 4. A value of .0625 is used for the radius, and .0313 for the thickness. The thickness value is only fifty millionths of an inch thicker than the nominal 1/32" thickness, so they think nothing of it.
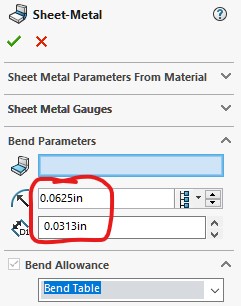
Image 4: Entering parameters.
This is when the errors start. As can be seen in Image 5, the error shows that the bend thickness falls outside of the bend table. It's a very accurate error message, and it is telling us exactly what is happening.
Image 5: Errors in a sheet metal part.
Fixing The First Problem
All the designer needs to do in this case is make sure the thickness of the part matches the table. That's it, nothing more, but they must be exactly the same. This is because of the inflexibility of the table, which we will get to in a moment.
The designer sets the thickness of the model to exactly .03125", and the first set of error messages disappear. This model is slightly outside the norm for the manufacturer because it has extra features they don't usually incorporate into their models. The first set of warning symbols are gone, but other errors related to miter bend and hem features remain.
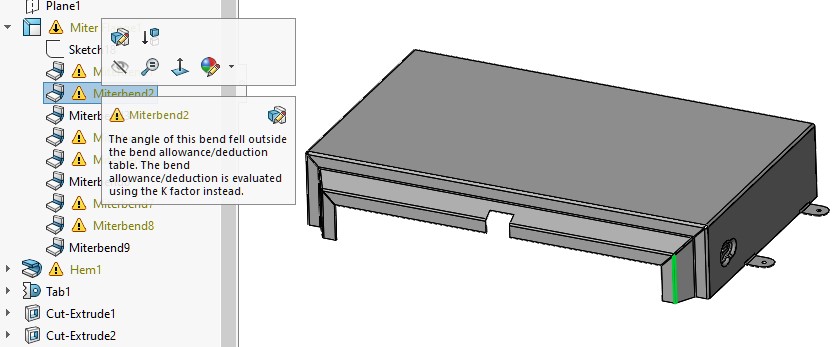
Fixing The Second Problem
This second problem, shown in Image 6, tells us the angle of the bend has fallen outside of the table. Of course it did! We only accounted for 90 degree bends. The hem in the model has a 180 degree bend, and the miter flange has 60 and 120 degree bends.
The nice thing about bend tables is that entering exact values is not necessary as long as the bend radius, bend angle, and material thickness fall within the parameters of the table. That is what is meant when referring to flexibility.
It's All About Interpolation
Not all of the sample bend tables included with SOLIDWORKS specify bend allowance. Some specify bend deduction or K-factor. The formats may be slightly different, but there is one overarching rule that should be followed. Always build the table large enough to encompass any possible parameter that may be used in your SOLIDWORKS sheet metal parts.
Let's rephrase and reiterate that main point, because it is worth repeating.
As long as the bend radius, bend angle, and material thickness fall within the parameters of the table, they do not have to match exactly what is specified in the table. Image 7 shows a slightly expanded version of the table shown originally in Image 3.

Image 7: Expanded bend table allows for greater flexibility.
With the newly expanded table shown in Image 7, the material thickness can be anywhere from .030 to .0625 inches, the bend angle can be anywhere from 30 to 180 degrees, and the bend radius can be anywhere from .0001 to .125 inches. If any of these 3 sheet metal parameters are not exactly what is listed in the bend table, SOLIDWORKS will interpolate between the existing values and come up with a new value.
Why have such a small bend radius of .0001" in the table? That's to account for our hems.
Bend tables don't have to be difficult. They just need to contain enough data for SOLIDWORKS to come up with an answer for you.
Click here to learn more about SOLIDWORKS gauge tables.
Click here to learn about sheet metal forming tools.